トヨタ生産方式の基本をわかりやすく解説!かんばん方式の図解付き
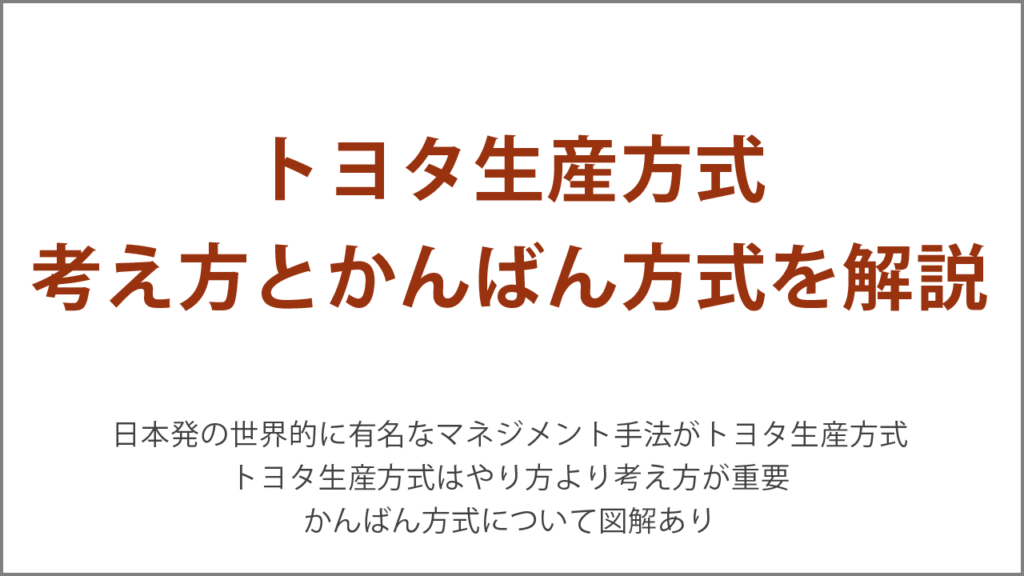
トヨタ生産方式は言うまでもないくらいに世界中に知られた日本初のマネジメント手法です。
マネジメントを学ぶ方が勉強していることが多いですし、昨今普及しているアジャイルにも取り入れられています。
今回はトヨタ生産方式の基本的なところについて解説します。主に考え方ややり方、メリットなどです。
そしてトヨタ生産方式が目指す目標であるジャストインタイムの実現において、特に重要なかんばん方式について図解付きで解説します。
マネジメントを学びたい方やトヨタ生産方式を学びたい方、効率化や無駄の削減ができる方法を探している方の参考になれば幸いです。
トヨタ生産方式とは
トヨタ生産方式とはトヨタが生み出したマネジメント手法です。生産方式ですので、工場で効率的な生産を行うための手法です。
考案者は当時の工場の責任者だった大野耐一という人物です。大野耐一本人が書いたトヨタ生産方式の書籍も出ており、1978年に初版が出たのにも関わらず、2024年になっても増刷されています。

トヨタ生産方式 脱規模の経営をめざして/大野耐一【1000円以上送料無料】
この書籍によると、トヨタ生産方式は創業家がジャストインタイムを実現すると宣言し、その実現方法を大野耐一が現場でひたすら10数年もかけて繰り返したものです。
そのような長い年月に渡る試行錯誤、そして現場の反発もあって、ようやく出来上がったのがトヨタ生産方式です。
そんな大変な思いをして作ったマネジメント手法ですので、是非ともありがたく使わせていただきたいところです。
トヨタ生産方式の考え方
トヨタ生産方式はやり方だけ真似しても上手くいきません。考え方が重要です。そこでこの記事ではまずトヨタ生産方式の考え方について解説します。
無駄の排除に重点を置く
トヨタ生産方式では無駄の排除に重点を置いています。
トヨタ生産方式が目指すのはジャストインタイムの実現です。必要なときに必要なものが必要なだけある状態です。これは無駄が全くなくて、理想的なまでに効率的な状態です。
ジャストインタイムを実現するためには、余計な在庫を持たず、必要なだけ生産する必要があります。
また必要なときに必要なだけの部品が必要ですので、欲しいと思ったらすぐに作れるリードタイムの短さも必要になります。
トヨタ生産方式ではこれらを実現するべく、作りすぎの無駄や動きの無駄などを排除していきます。
無駄の中でも大野耐一が特に恐ろしいと言っているのが、作りすぎの無駄です。
作りすぎの無駄をすると、時間、コスト、労力を余計にかけた上に、在庫を余分に持ってしまいます。在庫が多いと管理コストや保管場所のコストがかかります。
作りすぎの無駄はコストの増加につながるのです。
従業員を多能工にする
トヨタ生産方式では生産性を高めるために従業員を多能工にします。
従来であれば、従業員は役割分担され、自分の専門領域だけスキルを高めればいいという話になります。
しかしトヨタ生産方式では従業員は複数の職能をこなすことを求められます。単能工ではなく多能工になることを求められるのです。
これは生産性の向上やチームプレイでの助け合いにつながりますが、同時に自力で色々な仕事をこなせるというやりがいにもつながります。
もちろん勉強することが増えるので従業員からの反発はあります。しかし結果的には色々こなせる方が活躍の場を増やせますし、人繰りもしやすくなります。
チームプレイを重視する
経験が浅い従業員を助け合い運動と呼ぶ活動によって助けたり、多能工にして他の従業員を助けられるスキルを身に付けさせたりと、トヨタ生産方式ではチームプレイを重視しています。
後で解説するアンドンやなぜなぜ5回分析もみんなで問題について考える方法です。
かんばん方式はある意味ではリレー方式です。前工程の人と後工程の人の間でリレーが行われ、リレーによって全工程がつながっているのです。
私の個人的な意見ですが、多能工とチームプレイはつながっています。そして働きやすさにもつながる可能性があります。
もし単能工だったら他の従業員が困っていても、それは自分の担当じゃないから助けられないということになってしまいます。
しかし多能工であれば、助けることができる可能性があります。助け合いが職場に根付けば、働きやすさにもきっとつながります。
トヨタ生産方式で使われる方式
自働化
トヨタの創業者は豊田佐吉という人物です。トヨタ自動車ではなくトヨタ紡織を作った人物です。
https://www.toyota-shokki.co.jp/company/history/toyoda_sakichi/index.html
この豊田佐吉という人物が紡織機械で採用した仕組みが自働化です。
自働化とは自動運転する機械に問題が発生したら、機械が自動的に停止する仕組みです。これにより不良品を作ってしまうことを防げます。
自動運転するからと言っても、人間が目を離したときに機械に問題が発生して、そのまま動き続けたら不良品が量産されてしまいます。
これでは人間が機械を見張っていなければいけないので、人間の手が空きません。人間の所要工数はそのままに、機械が代わりに作業しているだけです。
つまり自動化では結局人間ができる仕事が増えないので、生産性の向上につながりません。
そこで自働化によって問題が発生したときは機械が自動的に止まる仕組みになっていれば、人間は機械を見張らなくてよくなります。
トヨタ紡織では若い女性が1人で40~50台の機械を担当していたそうです。
1人でこんなにも多くの機械を担当できた理由は、問題が発生したら自動的に止まるため、最初と最後だけ機械を操作すればよかったからです。
多工程持ち
どんな仕事でもそうですが、従来は1人1工程で専門家されていました。しかしトヨタ生産方式では1人で複数の工程を持ちます。
もちろん従業員からすれば専門外のことを勉強しなければいけないので、反発はあります。
しかし多能工になって複数の工程を担当できるようになれば、先ほども書いたように、人手が足りない工程を手伝ったり、経験が浅い人が苦戦しているのを助けたりできます。
多能工になることで従業員同士で助け合いが可能になるのです。
そして単能工では与えられた仕事をこなしているだけですが、多能工なら仕事全体を広く見ることができて、視野を広げられます。これがやりがいにつながるのです。
かんばん
かんばんはどの部品をいくらくらい作るかという指示を書いたものです。ジャストインタイムを実現する上でとても重要な道具です。
大野耐一がトヨタ生産方式を開発していた当時は、紙に印刷してビニール袋に入れていたそうです。
かんばんには生産指示かんばんと引き取りかんばんがあります。ざっくりと書くと以下のような流れになります。
- 後工程の担当者が引き取りかんばんを持って、前工程へ部品を取りに行く。
- 後工程の担当者は生産指示かんばんが付いた部品から生産指示かんばんを外し、引き取りかんばんを付けて、自分の作業場所へ持ってくる。
- 前工程の担当者は生産指示かんばんが外れていたら、生産指示かんばんに書かれた部品を書かれた数量だけ作る。作り終わったら生産指示かんばんを部品に付ける。
- 後工程の担当者は持ってきた部品から引き取りかんばんを外し、持ってきた部品を使って作業を行う。この後1.に戻る。
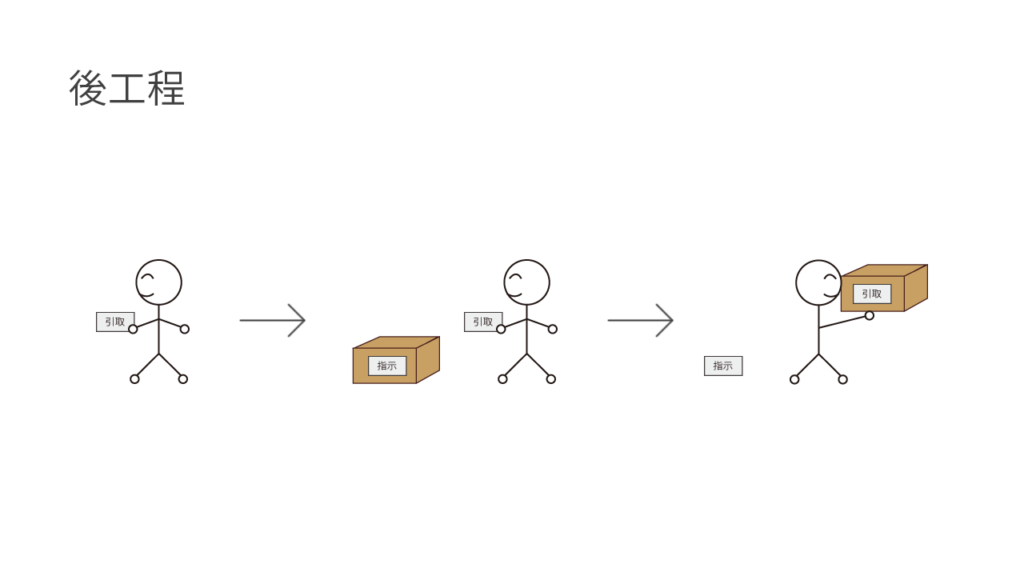

アンドン
生産ラインに異常が発生したときに、異常を知らせる表示板がアンドンです。
もし生産ラインに異常が発生すると、不良品を作り続けたり、生産が止まってしまったりします。いずれにせよ問題が発生した工程より後の工程の人たちに大きな影響を与えます。
そこで異常が発生したことを知らせる仕組みがアンドンです。アンドンに異常が表示されたら、みんなで問題を解決するのです。ここでもチームワークが重要なのです。
なぜなぜ5回分析
なぜなぜ5回分析は色々なところで聞きますので、有名でしょう。
5回である必要はないのですが、大体5回くらい原因を分析していけば、根本的な原因に辿り着けるという経験則から、なぜかを5回分析しろということです。
なぜなぜ5回分析はその場しのぎではなく、根本的な問題解決をするときに役立つ手法です。
かんばん方式でジャストインタイムを実現するメリット
在庫のコストを削減できる
ジャストインタイムを実現する上でとても重要なのが、かんばん方式です。かんばん方式を使ってジャストインタイムを実現すると、在庫のコストを削減できるというメリットがあります。
在庫が多いということは、保管する倉庫のコストがかかるということです。自社所有なら土地の購入費や建物の建設費がかかります。賃貸なら家賃がかかります。
また在庫を運搬する工数もかかります。もし倉庫が離れた場所にあれば、運搬に料金がかかるかもしれません。
さらには在庫の管理コストもかかります。何が何個あるか、古いものは何かなどです。
また在庫も帳簿上は、完成品なら棚卸資産、部品なら部品、製作途中の半完成品などなら仕掛品として計上する必要があります。そして決算書にもそれらの合計金額が載ります。
これらの理由ゆえ在庫はとてもコストがかかるのです。だからかんばん方式でジャストインタイムを実現して在庫を削減できると、大きなメリットがあります。
管理工数を削減できる
かんばん方式は後工程から前工程へ部品を引き取りに行く方式です。
ということはかんばん方式では最終工程だけ計画作成や進捗管理をすればいいのです。他の工程は自動的に決まるからです。
かんばん方式ではない従来型の、前工程から後工程へ流していく生産方式ですと、全工程の生産計画を立てて、全工程の進捗管理をする必要があります。
これでは管理工数が膨大に大きくなってしまいます。
実はかんばん方式でジャストインタイムを実現することで、管理工数を大きく削減できるのです。
終わりに
今回はトヨタ生産方式について基本的な考え方や方式を解説しました。またトヨタ生産方式において特に重要なかんばん方式について、図解しました。
トヨタ生産方式は生産性や効率、無駄や在庫の削減という点において、とても有効なマネジメント手法です。マネジメントを勉強している人たちの間でも、定番の知識です。
だからトヨタ生産方式を知っておいて損はないと私は考えています。
有効な知識をしっかりと活用して、仕事をいいものに変えていきましょう。