部分最適ではなく全体最適によって生産性を上げよう
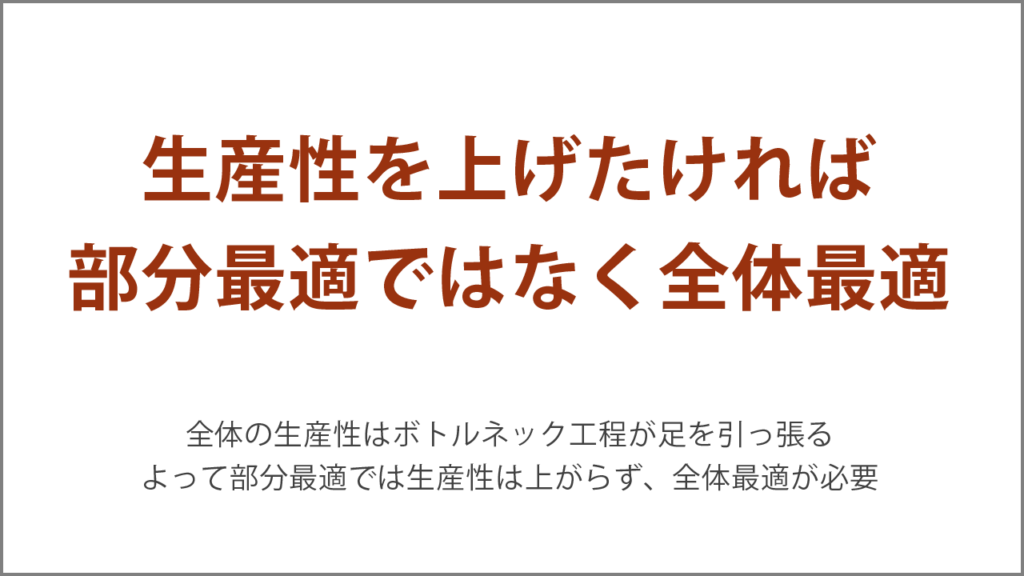
今回は生産性を上げるために必要な考え方を解説します。それは部分最適ではなく全体最適を行うということです。
目立つ作業や改善しやすい作業、あるいは自社の強みを活かせる業務にばかり注力して、そればかり改善や強化をし続けてしまうケースがあるかもしれません。
しかしそれでは特定の作業の生産性は上がりますが、最終的な成果物は増やせません。つまり一見生産性は上がったようで、本当に生産性が上がったとは言えないのです。
今回は生産性を上げるためには全体最適が必要である理由を解説します。次のような方に参考にしていただければ幸いです。
- 生産性を上げたいという方
- 業務改善に取り組む方
- マネジメントに携わっている方
- 生産性を上げるヒントが部分最適と全体最適らしいと知った方
それでは始めましょう。
部分最適と全体最適について
部分最適とは
部分最適とは一部の作業や工程だけを最適化、すなわち問題や効率の改善を行うことです。
大抵の仕事には流れがあります(業務フローと呼んだりします)。
次のような4つの工程がある業務を考えてみましょう。ここで工程2だけ無駄の削減やツールの導入によって生産性を上げたとします。
これが部分最適です。工程2に携わる従業員は、作業効率がとても上がって、残業時間も減りそうです。人を余すくらいになるかもしれませんので、他の工程を手伝うことになるかもしれません。
これは一見いいことに見えますが、実は問題があります。それは後程解説します。
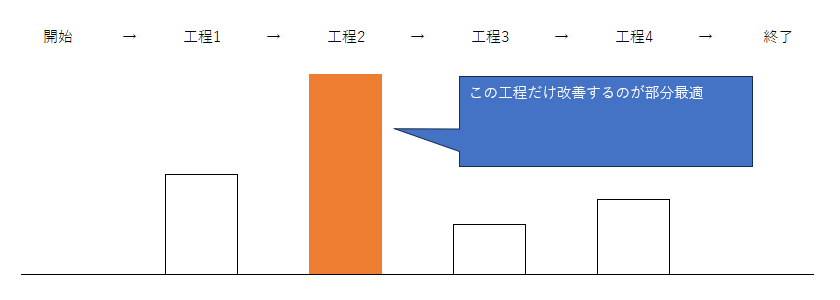
全体最適とは
全体最適とは全ての工程を総合的に見て最適化、すなわち全工程を通しての問題や効率の改善を行うことです。
部分最適と同様に4つの工程がある業務で考えてみましょう。先ほどは工程2だけ極端に生産性が高くなっていましたが、今度は全体が同じくらいになっています。
このように全工程を改善する方が全体最適と言えます。そして生産性を上げるには全体最適をした方がよいです。その理由も後ほど解説します。
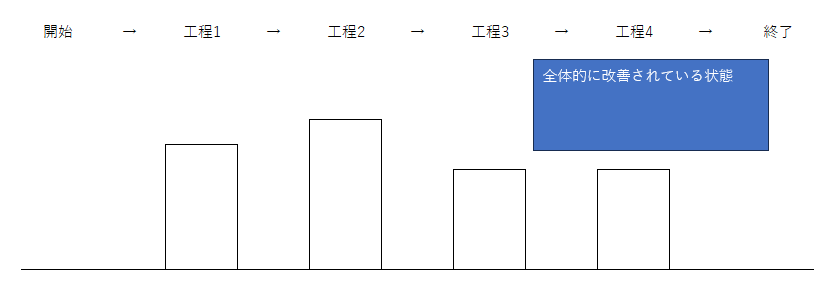
生産性とは
生産性の定義
生産性とは一般的には、一定時間に一定人数で作れる成果物の量を指します。サービスなら一定時間に一定人数でこなせる成果の量と考えてよいでしょう。
具体的にするため、おにぎりを作る仕事で考えてみましょう。この場合、例えば1時間に1人が作れるおにぎりが100個だとすると、1時間当たり1人当たりの生産性は100個となります。
これが型を使って効率化したら1時間当たり1人当たり120個作れるようになったとします。そうすると生産性は100個から120個に上がるので、20%アップとなります。
生産性を上げるメリット
生産性を上げるということは、作れるあるいはこなせる成果が増えるということです。成果が増えると売上を増やせます。
ということは生産性が高ければ高いほど売上が増えるのです。売上が増えると変動費は増えますが、固定費は一定です。よって限界利益がプラスでさえあれば、生産性が高いほど利益が増えます。
利益が増えるということは業績がアップするということでもあり、手元に残るお金が増えるということでもあります。すると設備やITなどの投資に回したり、従業員の給料やボーナスに反映したりできます。
設備やITなどに投資すれば更に生産性を上げられますし、従業員からすれば給料やボーナスが増えれば嬉しいでしょう。生産性を上げるメリットはとても大きいです。
また見方を変えると、今まで残業して売上を稼いでいたのが、残業せずとも同じ売上を稼げるようになる可能性もあります。生産性を上げると残業削減にもつながるのです。
ところでここで変動費、固定費、限界利益という言葉がでてきました。もしあなたが会計を勉強したことがない場合、こちらに解説を書いていますので参考にしてください。
変動費と固定費はこちらの記事で解説しています。
限界利益はこちらの記事で解説しています。
生産性を上げるには部分最適ではなく全体最適を行う
部分ではなく全体の生産性を上げることを意識する
最初に断っておきます。生産性を上げたいなら部分最適ではなく全体最適を意識しましょう。
現実には部分最適ばかり行ったり、ツール(ロボットやAIなど)さえ使えばいいと考えたりする例が多いです。しかしそれでは生産性は上がりません。
業務フロー図を描くなどして、業務の全体を把握するように心がけてください。業務全体を把握できている人は意外と少ないので、部分最適に陥りがちなのです。
またシャイニーオブジェクト症候群という、新しいテクノロジーや他社の成功事例を魅力的に感じて、テクノロジーを使うことを目的にしてしまう危険性もあります。
ネットで情報を収集しやすくなった現在、シャイニーオブジェクト症候群は至るところにあふれています。こちらの記事でもシャイニーオブジェクト症候群を解説していますので、どんなものか気になったら読んでみてください。
https://note.com/irohas_diary/n/ne0bef58a9bd3
ツールを使うことが目的化すると最悪です。導入したけど使えないとか、導入に時間やお金がかかりすぎて導入が進まないということが起こりがちです。
部分最適をしても全体の生産性は上がらない
部分最適では生産性が上がらない理由は制約理論(TOC)で説明できます。
ザ・ゴールというビジネス小説で制約理論が解説されています。
制約理論とはボトルネック工程の生産性が全体の生産性を引っ張るという理論です。
あなたもボトルネックと言う言葉を聞いたことがあるかもしれません。仕事では最も生産性が低い工程をボトルネック工程と呼びます。そしてボトルネック工程が全体の生産性の足を引っ張ります。
これが部分最適では生産性が上がらない理由です。生産性を上げようと思ったら、ボトルネックを解消して全体の生産性を上げる必要があるのです。
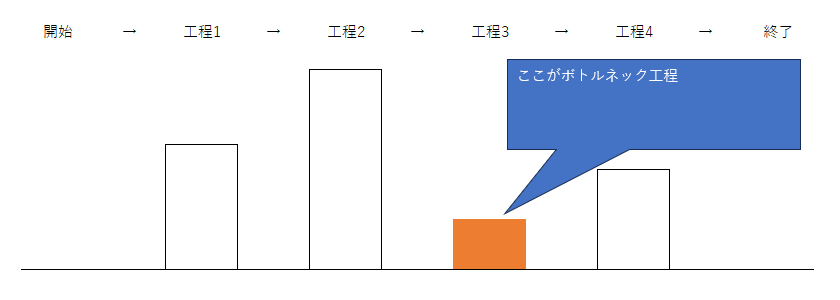
ザ・ゴールという小説では制約理論をボーイスカウトのハイキングで解説しています。体が大きな少年が山登りで一人だけ遅れてしまいます。みんな待ちくたびれてしまいます。
ここでボトルネックはこの体が大きくて遅れた少年です。そしてたとえ歩くのが速い登山部や陸上部の子を連れてきても、全体のペースは上がりません。なぜなら遅れている少年を一人だけおいていくわけにはいかないからです。
つまりボトルネックのせいで他がどれだけ速くても、全体としては遅くなってしまうのです。
あなたも何か特定の遅いものが足を引っ張った経験はありませんか?あるいは学業や資格試験で、極端に点数の低い科目が足を引っ張った経験はありませんか?
生産性を上げたいときは、ボトルネックに着目して全体の生産性を意識してください。
ザ・ゴールはマネジメントを学ぶ人の多くが読んでいるくらい定番のビジネス書です。生産性を上げる方法を学びたいなら是非読んでみてください。

ザ・ゴール 企業の究極の目的とは何か【電子書籍】[ エリヤフ・ゴールドラット ]
全体最適をすれば全体の生産性が上がる
ボトルネック工程を改善する
先ほどのザ・ゴールの例でいうと、遅れている体が大きな少年の荷物をみんなで持ってあげるとか、この少年を先頭にして自分のペースで歩きやすくしてやることで、誰も遅れなくなります。
ボトルネック以外の工程が多少は非効率になってでも、ボトルネック工程の生産性を上げることが重要です。こうすることで全体の生産性が上がります。
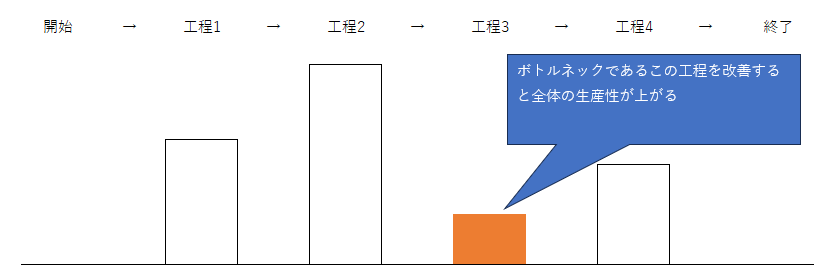
全体最適を行うためには業務フロー全体を見渡す必要があります。先ほども書きました通り、業務フロー図を作るのが良いです。
まずは現状の業務を洗い出して業務フロー図を作ります。そして各業務フローの中で、生産性を下げている要因を洗い出しつつ、各工程の生産性を調べて行きます。
1日当たりの成果物の量を測ると生産性が解りやすいでしょう。製造業なら作った数、物流業なら次の工程に送り出した数、オフィスワークなら作ったデータや資料の数が解りやすい成果物です。
こうしてボトルネック工程を洗い出し、ボトルネック工程を改善していきましょう。ボトルネック工程を改善すると、別の工程がボトルネック工程に変わることもあります。これはボトルネック工程を1つ解消できた証拠です。
クリティカルパスを意識する
またクリティカルパスも意識してみるとよいでしょう。クリティカルパス上にある作業の工数を削減できると、業務フロー全体を通しての最低工数を削減できます。逆にクリティカルパス上にない作業を改善しても、業務フロー全体を通しての工数は削減できません。
クリティカルパスについては別途記事を書いていますので、参考にしてみてください。
全工程で生産性を同水準にすることを意識する
トヨタ生産方式が有名で効果を発揮していることは今更言うまでもないでしょう。
トヨタ生産方式でも速い工程をあえて遅くすることで、全工程の生産性を同程度にしています。プレスのような同じ金型で量産した方がいい工程でも、あえて段取り替え(作る部品に合わせた機械のセッティング変更)を行うことで生産性を下げています。
トヨタ生産方式ではジャストインタイムが重要視されています。必要なものを必要なときに必要なだけ作るのです。それを実現するためにかんばん方式を使い、後工程から前工程へと部品を取りに行きます。そしてトヨタ生産方式では部品を後工程に渡した分だけしか作りません。
ということは前工程の方が後工程より生産性が高いと、前工程では人が待機する時間が増えます。逆に前工程の方が後工程より生産性が低いと、後工程が部品を取りに来ても、部品を渡すことができません。
ジャストインタイムとかんばん方式を成立させるためには、全工程で生産性が同程度になっている必要があるということです。
トヨタ生産方式も生産性を上げることに役立ちますので、興味があれば是非とも本を読んでみてください。提唱者にして構築者である大野耐一氏の書籍が、1978年発売からずっと増刷され続けているくらい読まれている書籍です。

トヨタ生産方式 脱規模の経営をめざして/大野耐一【1000円以上送料無料】
また図解入門シリーズにもトヨタ生産方式があります。手軽に図解で解りやすく読みたいなら、このシリーズはおススメです。

図解入門ビジネス最新トヨタ生産方式の基本と実践がよ~くわかる本[第2版] [ 石川秀人 ]
終わりに
今回は生産性を上げたいという方のために、部分最適では生産性が上がらない理由、そして全体最適をする必要がある理由を解説しました。
生産性を上げるメリットはとても大きいですし、人手不足は世界的な傾向です。よって限られた人員で成果を上げる必要があります。そうなると益々生産性を上げる必要があります。
是非とも生産性を高めて健全な働き方実現してくださいね。